Building Robust Drone Manufacturing and Supply Chain Capabilities in the USA
Avoid drone design and production issues while saving time and money whether you build in-house or source EMS manufacturing services. Includes multiple links to support articles and resources that help vendors and suppliers become more proficient solving problems facing drone manufacturers.
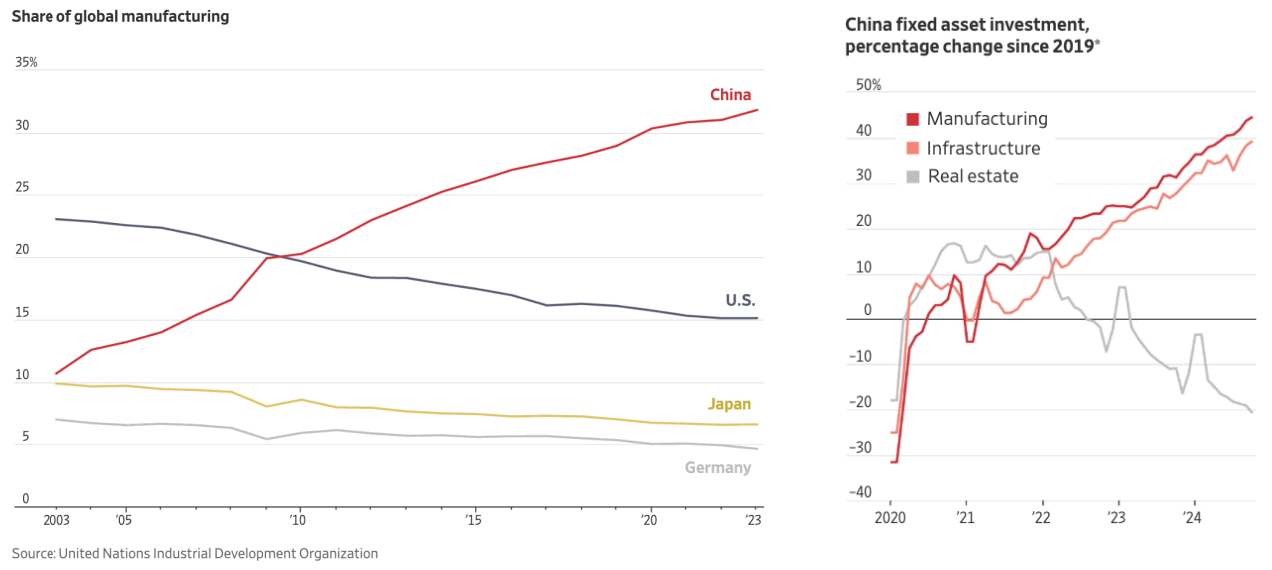
The U.S. Pacific Northwest is home to innovative mixed technologies manufacturing. This has been driven considerably by US government spending, particularly for military and defense programs.
Most of my readers know, depending on the target industry or market, creating successful electronics industry and manufacturing hubs requires lots of industry- and market-specific supply chain vendors and suppliers to be located nearby. You see first-hand why this ecosystem-moat combo builds your confidence you can get your work done. You also see how it helps attract, develop and retain regional commerce and grow government tax receipts.
Contrary to what many might know today, China still remains the world center for electronics manufacturing of components and assemblies. For drone manufacturers, you probably already know much of the technology and many parts used in the production and manufacturing of drones comes from China.
Drone Technology Origin vs Country of Manufacture
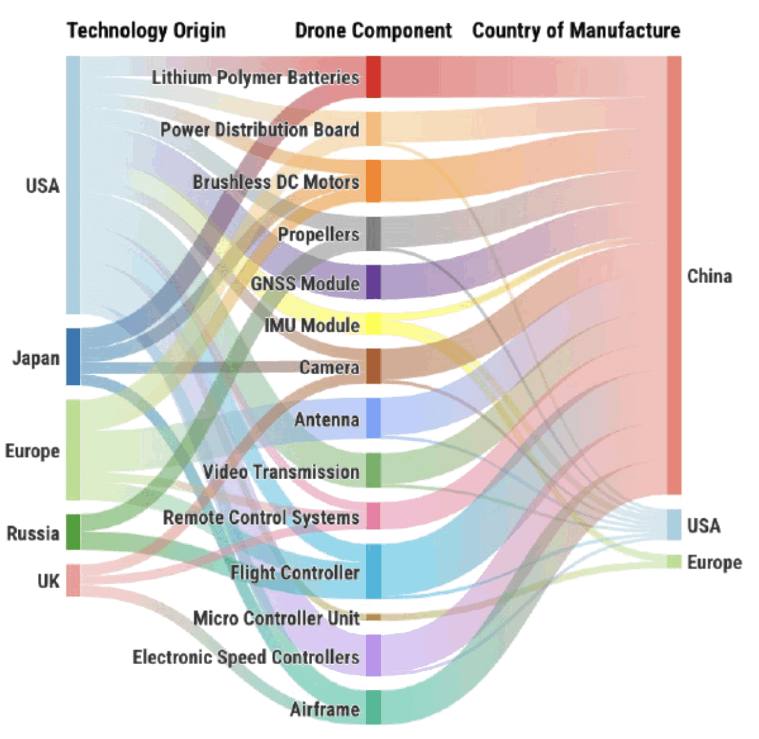
In fact, the world's largest drone manufacturer is DJI and it is headquartered in Shenzhen, China. China built a successful ecosystem for its drone industry.
Closing the Gap in US Drone Manufacturing Supply Chains
I'm familiar with enough drone manufacturing programs to have a good idea about what's important. This article can serve as a knowledge resource or guide for U.S. drone manufacturers and vendors and suppliers serving U.S. drone manufacturing companies so all parties can prosper.
For drone manufacturers focused on achieving competitive target pricing of their products through reduction of your operating overhead costs through outsourcing, matching your program's technical and manufacturing requirements with your CM or defense prime will always be on your short list of 'must haves'.
Drone design and manufacturing requires specialization. Specialization is key when identifying supply chain partners for niche industries. When done properly, together, you can boost productivity enormously. This has been known for years and was first put into context in Adam Smith’s 1776 opus, An Inquiry into the Nature and Causes of the Wealth of Nations - better known as - The Wealth of Nations.
Drone, UAV, UAS. What’s The Difference?
Drone
By its simplest definition a drone can be defined as any vehicle that can be controlled or piloted without a pilot or ‘driver’ inside it. Categorizing a drone is not limited to something that becomes mobile and flies in the air. Drone can also be applied to vehicles that move on land and in water where mobility is also without a driver inside the vehicle.
Unmanned Aerial Vehicle (UAV)
UAV refers to a vehicle or aircraft that takes to the air and can fly remotely or autonomously.
One main distinction between drones and UAVs is not every drone is a UAV whereas every UAV can be a drone. UAV also takes into consideration the entirety of the vehicle – the aircraft itself.
Unmanned Aerial System (UAS)
UAS refers to elements within and associated with the vehicle enabling it to perform or fly. These include control computers for flight (and auto pilot), mission computers and control stations, other aviation and avionics hardware and the perhaps input from person(s) manipulating the ground control module, software and communications systems, navigation systems and GPS modules, cameras and transmission systems, and assemblies, subassemblies, electro-mechanical systems, components. You get the idea.
Drone systems can be designed for long endurance flight vehicles whereas some drones may contain hydrogen fuel cells or be gas hybrid or tethered depending on the UAV capabilities customers and the purpose the drone is selected for.
Training and piloting skill also fall into the UAS category.
Drone Design and Components Considerations
Drone electronics product design, whether it's for consumer or military drones, or large agricultural machinery, or embedded electronics inside automobile cabins... trend toward higher degrees of functionality and smaller footprint.
This combination, especially when combined with new and evolving material composites plus, fit/form/function requirements, offer a lot of new opportunities for drone engineers and customers.
Drone design considerations are especially important for military aviation and space applications where lightweight and small footprints and energy consumption are closely tied together.
Add to this, how drone systems perform is also related to available bandwidth and processing power. As processors become more powerful drone engineers have to take into consideration high-speed and board-level interconnects. Size constraints here can boost engineering ability to achieve higher connector contact densities supporting optical interconnects and RF – at the circuit board level.
Add to this, drone circuit boards are often crammed with components with an abnormally high number of connector pins necessary for the equally high number of external signals. Finding this balance between drone technical specs and pushing physical hardware constraints is not easy for drone engineers to accomplish.
Altitude
Drones designed to achieve higher altitudes need different component requirements. For example, electrolytic capacitors are not good. Electrolytes are liquid, or gel, with a high concentration of ions. Lower atmospheric pressure at higher altitudes can be problematic because electrolytic capacitors will expand and leak causing the capacitor to fail. In addition to a limited lifetime electrolytic capacitors also have large value tolerances.
At the printed circuit board (PCB) level wider route trace spacing is often needed for higher voltage signals especially as arc potential increases in lower pressure environments above 20,000 feet. Drone designers enjoy figuring out challenges posed by trace routing, giving designers opportunity to solve sometimes as complicated and unique puzzles, especially as board design functional complexity increases with smaller footprints.
_________________________________________________________
About
What matters when formulating contract electronic strategy? How do you identify supplier profit centers and what are you doing to protect against margin erosion for your outsourcing programs? Why do provider capabilities often not match capabilities they claim? How are you benchmarking your supply chain against competitors?
I’ve spent 25+ years in contract electronics industry setting up contract electronic divisions and running operations, protecting EMS program profits, manufacturing capacity M&A and more. I run a technology solutions firm. A lot of times this means asking the right questions.
_________________________________________________________
Drones achieving varying altitudes during flight will also experience hot and cold cycles with temperature fluctuations. Drone electronics and sub-systems with conformal coating applied on top of circuit boards and components helps guard against altitude cycling failure because conformal coating lets any air trapped beneath ICs expand at higher altitudes.
One way CMs, defense primes or EMS manufacturers might help drone manufacturers minimize this risk is applying ‘coatings’ in a low-pressure chamber. This helps remove air voids trapped underneath parts and components.
Temperature
The operating temperature range a lot of drone motors typically operate within is similar to automotive engines, -40C to +80C, although a good percentage of drones on the market today, by volume, are more likely to operate in the higher end of this range vs the lower end. Power design for the ideal drone is able to cover a broad range while being dependent on market vertical and customer needs.
From a PCB designer perspective, larger boards are usually easier to keep from overheating but smaller boards, while not always as thermal-friendly, are more aligned with many drone manufacturers' packaging and enclosure consideration. I write more space efficiency and portability, below.
Sensor technology
Sensor technology is becoming more intelligent and drones using this provide user benefits like avoiding, or targeting, air and land objects achieved by hovering and maneuvering with help from sensors. As an example, digital barometric pressure sensors allow drones to perceive altitude and to stabilize. Precision drone flight using sensor technology is further aided by a drone's gyroscope and accelerometer.
Some other common drone sensor technologies used today calculate and measure humidity (atmospheric and drone internal) and drone position.
Drones processing atmospheric info can be attributed directly to success in some applications like as agricultural spraying. As an agricultural drone travels faster its spraying application requires even distribution while not over-spraying which can result in costly waste and application levels higher than wanted.
Drones able to sense atmospheric data tied to airspeed can also compensate for changes in lift force and drag force, which impacts rate and volume of application.
Drones deploying measurement technologies using mounted sensors on PCBs will depend on printed wiring board, drone configuration and space limitations for each decided on by PCB and drone designers.
Shielding and low EMI layouts
Most drones will have some type of communications signal, while most electronics are prone to radio frequency interference (RFI) or electromagnetic interference (EMI), which can decrease circuit performance or even cause failure. Good drone designers work on programs while being aware electromagnetic fields can easily disrupt electronics systems, in various ways, with just small voltages and currents.
Add to this, advancing technologies in data processing and communications are introducing increasingly higher levels of interference to the electromagnetic wave spectrum, in addition to other problems like solar flares and lightning strikes. Some effects of EMI include:
· Electronic circuit damage or failure
· Electric shock and burns
· Power fluctuations and power outage
· Unusual or jammed signals received by communications devices